By the end of 2021, components for more than 4,000 offshore wind turbines had been shipped from Port Esbjerg, meaning the harbour had contributed to the development of more than 22.5 GW of offshore-based renewable energy since the first shipments in 2001. Two key players during the past decade offer congratulations and look both back and forward to the future.
Wind turbine number 4,000 being loaded at Esbjerg harbour in December was a special day. The turbine was then shipped out to sea to stand for many years and produce green energy, marking a milestone for all involved in the renewables business.
“Congratulations Esbjerg,” says Mikkel Gleerup, CEO of Cadeler A/S, a shipping services supplier to the offshore wind industry that has been located at the Port Esbjerg for many years.
“Things have gone well and have certainly gone very fast for the industry, which has progressed from infancy to mature business, and mostly in the past ten years. The 4,000 turbines are not only a huge milestone for Esbjerg, but for the entire sector,” says Mikkel Gleerup.
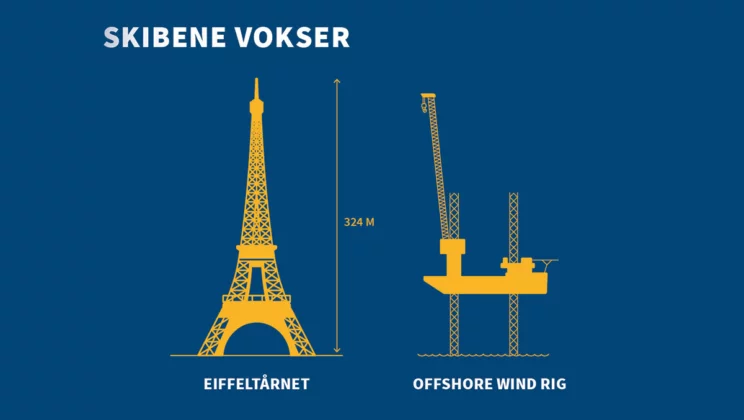
Turbines and offshore rigs are getting bigger and bigger.
Cadeler has also been developing ever more rapidly over the period.
“We are now a completely different company compared to 10 years ago, having grown dramatically from being a regional business to becoming a listed corporation with more than DKK 5 billion in equipment assets in 2021. We are now looking at potential opportunities outside Europe, which is the area we have so far focused on most. Naturally, we are constantly assessing opportunities in North America and Asia to determine whether or not they are attractive for Cadeler to engage with. Like Port Esbjerg, our focus is on growth and on acquiring new ships that can install the turbines of the future. Esbjerg is part of a well-functioning ecosystem where companies and the port work seamlessly together. Port Esbjerg is in fact one of the reasons for our success,” says Mikkel Gleerup.
According to Mikkel Gleerup, that ecosystem has been crucial both for past growth and for growth to continue in the coming years. Having 200 companies located in the port ensures that when a welder is needed, one can be found. If you need scaffolding, that is there too. If a health and safety system has to be approved, that is also taken care of locally.
“Esbjerg should do everything necessary to maintain its ecosystem. Esbjerg’s good geographical location and its ecosystem are a source of positive energy. The port houses forward-looking companies and that helps make us feel at home here, even though we are a global company. In my eyes, Esbjerg is the design basis for offshore wind ports around the world,” says Mikkel Gleerup.
Cadeler has just ordered new HOV cranes for its existing O-class vessels. Recent developments mean that whereas ships were previously loaded with 12 turbines of 3.6 MW, the turbines have grown so significantly that now the cargo is five 10 MW turbines, or four 15 MW turbines. Roughly the same number of MW is loaded but with fewer wind turbines. The company has also ordered two new X-class vessels, which will be among the largest installation vessels in the world. The arms of the new cranes on these ships will be 155 metres long and can reach 180 metres above the deck. They can also be further extended to 175 metres, so they can reach 200 metres above the deck.
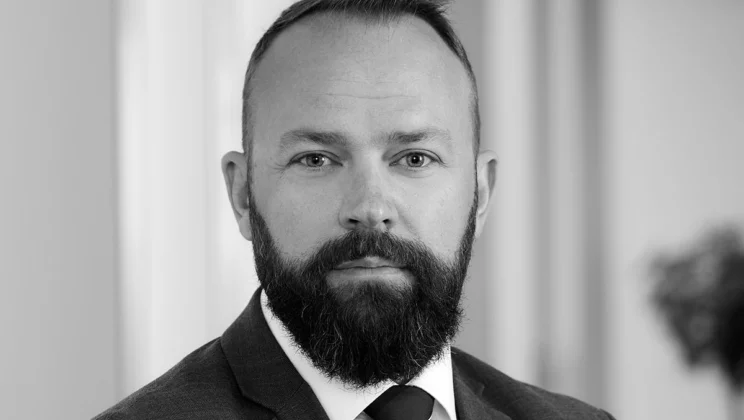
Mikkel Gleerup, CEO of Cadeler A / S looks back on the great development of Port Esbjerg.
Congratulations too from LM
Port Esbjerg received a second round of congratulations for the 4,000 wind turbines it has shipped. This time from LM Wind Power, which has also worked out of the port for many years. Jesper Sørensen says ‘well done’ – he is Senior Director for the Haliade X blade programme, a turbine platform for GE. He also lives in Esbjerg.
Emphasising each syllable, he says that the industry has almost ‘exploded’ in recent years.
“There has been a tectonic shift. From small, niche industry to mainstream, with China also expanding rapidly. Esbjerg has been far-sighted, ensuring logistics and storage are in place. There are now several harbours with room for manufacturing facilities in the immediate area, and that is an advantage now that blades are up to 107 metres long and with a root diameter of 5.5 metres.”
Jesper Sørensen says he becomes rather nostalgic thinking back to the 2000s when engineers were discussing whether the maximum blade length was 50 metres.
“Yet blades get longer and longer. No-one knows what the limit is,” he says.
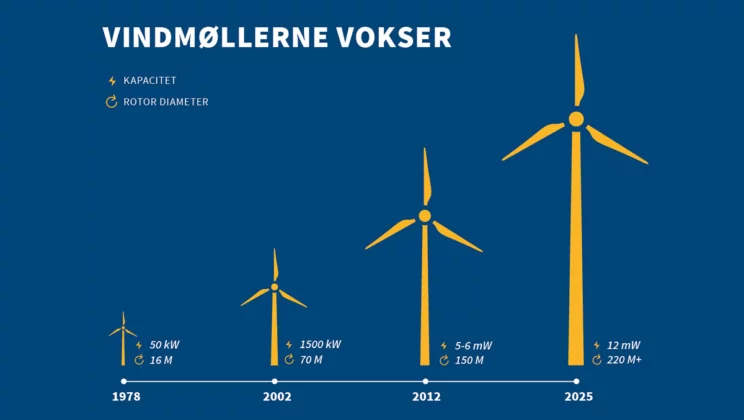
The size of offshore wind turbines has multiplied.
However, a particular challenge with scaling up is that doubling the blade length also makes the blade many times heavier. And heavier means more expensive, as greater amounts of material have to be used.
“The technological development supports larger blades, but the industry also has to ensure their financial viability and the logistics,” he says. “Transporting and erecting the turbines becomes difficult when they are so big and requires customised cranes and huge vessels”.
“This is where Port Esbjerg has been very forward-looking. There is room to expand in the harbour,” says Jesper Sørensen.
LM Wind Power has produced more than 250,000 blades. The majority of them in recent years.
A rule of thumb says that doubling the blade length generates four times as much energy, as twice the blade length means the turbine can cover four times the area and ‘capture’ much more wind. That is why a turbine like the Chinese MySE can produce five times as much power as, for example, the turbines we can see from the Great Belt bridge, even though it is nowhere near five times as large. The Chinese manufacturer states that one giant turbine can provide electricity for 20,000 households a year.
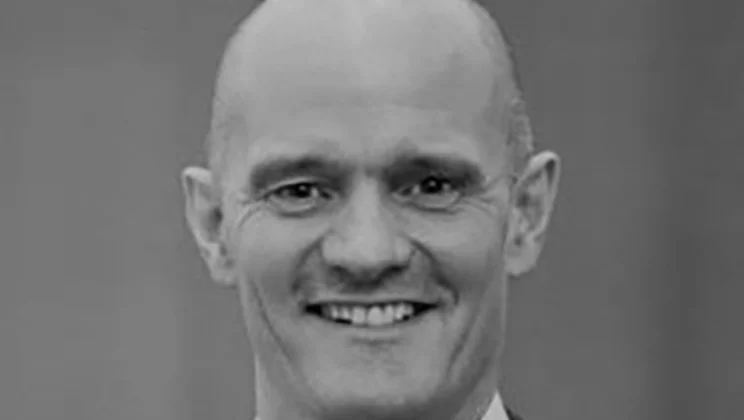
Jesper Sørensen, Senior Director at GM praises the port for foresight.
Eyes on the future
While there is reason to celebrate the impressive milestone, Port Esbjerg nevertheless has its eyes firmly on the future, as CEO Dennis Jul Pedersen, explains:
“We have come very far here in Esbjerg. But demand for offshore wind power will only increase, so our port infrastructure has to keep abreast of developments. We have to continuously make the processes around offshore wind projects in Esbjerg more efficient.”
One major initiative at the port is the construction of a pre-assembly site, where wind turbine manufacturers and project developers can assemble turbine components on the dockside prior to being shipped out into the North Sea. This will become crucial as turbines grow bigger and bigger – and at the same time it provides flexibility for project developers, who are only attached during the project period.
The concept has been developed in consultation with wind turbine producer Siemens Gamesa to ensure the best setup.
“This is an example of our aim to create optimal flexibility for our customers and partners,” says Jul Pedersen, before he turns to the more distant future.
“Getting the infrastructure and investment in place is one thing. But we also need young people to drive this enormous transformation of our energy supplies, which requires that we train the next generation.”
Port Esbjerg has in fact initiated a cooperative venture with Siemens to have in place a major offshore component that can be used as a training facility for student engineers and technicians. The idea is that doing this will mean the 4,000 offshore turbines already shipped out from the Port Esbjerg is merely the harbinger of the next 4,000.
Go to overview